Quality Assurance with AQL Inspection Plan – Guaranteeing the Quality of Your Products
At Pro China Direct Limited (PCD), we understand that trust and quality are of utmost importance to you, especially when sourcing products from China. That’s why we want to give you an insight into how we ensure that the quality of the products we deliver meets your requirements.
We use the internationally recognized AQL (Acceptable Quality Level) standard for this purpose. This method for determining the required sample size in quality management allows us to guarantee the quality of our deliveries.
The AQL method was developed by the US Army during World War II and is now standardized as DIN ISO 2859-1. It is based on a precise procedure where a defined sample is taken from a batch of goods, such as a delivery lot. This sample is then inspected according to established standards, regulations, and tolerances agreed upon between the supplier and the customer.
Understanding AQL Tables
In the AQL tables, it is precisely defined up to which number of defective products a batch can be accepted and from which number it will be rejected. At PCD, we use the following standard AQL values unless otherwise specified by you or our customer:
Critical defects: No critical defects are accepted.
Major defects: AQL 2.5
Minor defects: AQL 4.0
The AQL values are not expressed as a percentage rate but are rather a statistical distribution.
AQL Inspection Example: 8,000 Bags with General Inspection Level II
To better understand the AQL inspection system, let’s consider an example. Suppose we have an order of 8,000 bags to be inspected using the “General Inspection Level II.”
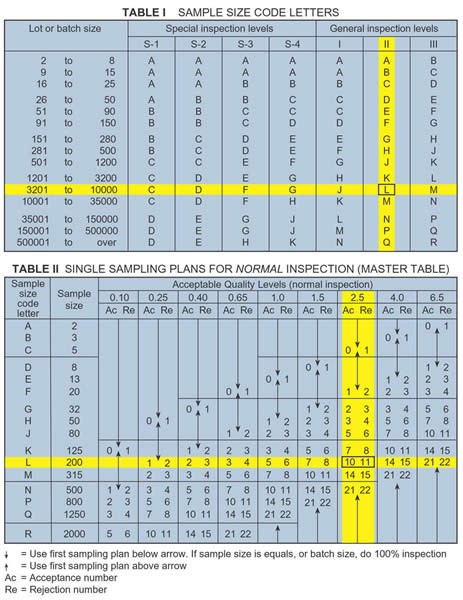
AQL Inspection Tables
First, we need to determine the “Sample Size Code Letter,” which is crucial for the sample size. For an order quantity of 8,000 bags and General Inspection Level II, the “Sample Size Code Letter” corresponds to the letter “L” according to the AQL table.
Now we use the “Single Sampling Plan for NORMAL Inspections” with the “Sample Size Code Letter” “L.” In the table, we find that for letter “L,” a sample size of 200 bags must be taken for inspection.
Assuming we have set an AQL value of 2.5 for major defects, the accepted defect rate (Acceptance Number) for AQL 2.5 is ten defective products according to the AQL table for the Single Sampling Plan for NORMAL Inspections and the letter “L.” The rejected defect rate (Rejection Number) is eleven defective products.
This means that during the inspection of the 200 sampled bags, if ten or fewer major defects are found, the entire delivery is considered acceptable. However, if eleven or more major defects are discovered, the entire delivery will be rejected.
By applying this inspection system, we ensure that the quality of the delivered products meets your expectations and any issues are detected early on.
Agreement of Defect Lists and Inspection Criteria
Our customers can specify which points should be classified as minor defects, major defects, or critical defects in a defect list. This, along with inspection criteria and product specifications, is agreed upon between the buyer and supplier before production begins.
Trusting in Quality through AQL
By applying the Quality Assurance with AQL Inspection, you can rely on us to meet your quality requirements even before your order is placed. Continuous quality checks and adherence to the AQL standard ensure that the delivered products meet your expectations.
Consultation and Support
If you have any questions about which standard should be applied to your products, we are happy to help. We will gladly advise you and find the best solution for your requirements together.
Contact
Contact Form